What is Phosphate Coating?
Phosphate coating in industrial scale; it can be defined as the process of phosphate coating solution forming an insoluble phosphate layer on a metal surface by dipping, spraying or any other method. For the formation of this type of coating, the content of the prepared solution must contain hydrogen ion (H+) for initial surface etching and providing proper pH, phosphate anion (PO4-3) and at least one metal cation to ensure the coating.
Zinc Phosphate Coating Scanning Electron Microscope (SEM) Image >>>
Phosphate Coating Reactions
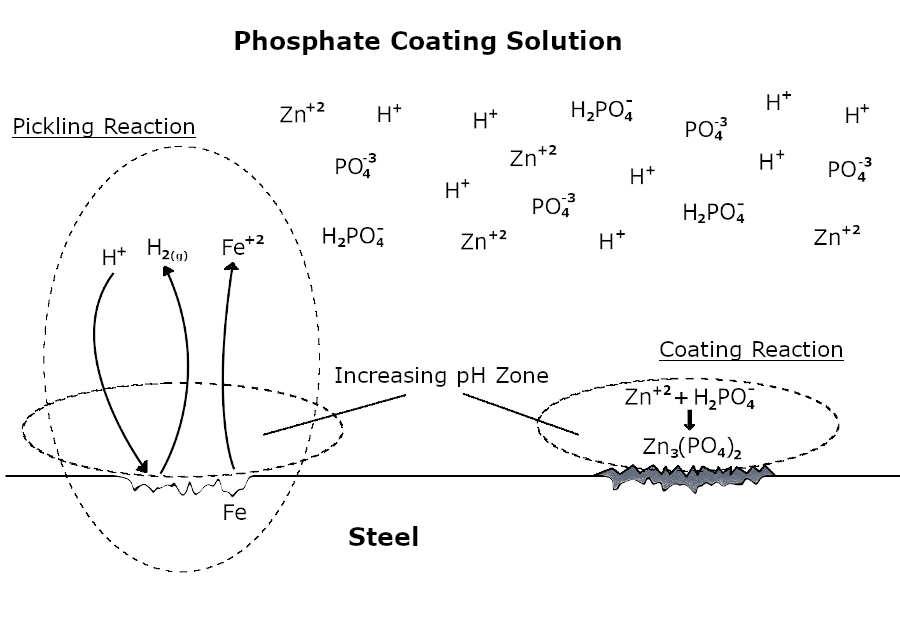
If a metal has the ability to react with an acidic phosphate coating solution, an etching reaction occurs primarily on the surface.
                          Fe   +   2H+   →   Fe+2   +   H2(g)
Subsequently, the pH increases as a result of neutralization in the region of the solution close to the metal surface. The soluble phosphate becomes insoluble in the rising pH region and phosphate coating begins to form as a result of crystallization.
                          3Zn+2   +   6H2PO4-   →   Zn3(PO4)2   +   4H+   +   4H2PO4-
This etching and coating process continues until the entire surface is covered with a phosphate layer. As soon as the phosphatizing solution does not have direct contact with the metal surface, the etching reaction and coating formation end.
Phosphate Coating Lines
For phosphate coating, the metal surface must come into contact with the phosphate coating solution. This contact is achieved mainly by dipping and spraying methods. Many issues should be taken into account when determining the appropriate method. The properties of the desired coating should be considered in detail for the working temperature, the shapes of the parts to be treated, the working intensity and the design of the application method and steps to the automation.
Process Bath Materials
Since the corrosive effects of alkaline degreasing solutions are not much, it is suitable for the bath material to be made of standard steel with protective coating or a hard plastic material such as polypropylene.
Although it is appropriate that the rinsing bath material is made of standard steel, it is recommended that the inner walls be coated with plastic in order to prevent corrosive effect, especially in the case of pure water.
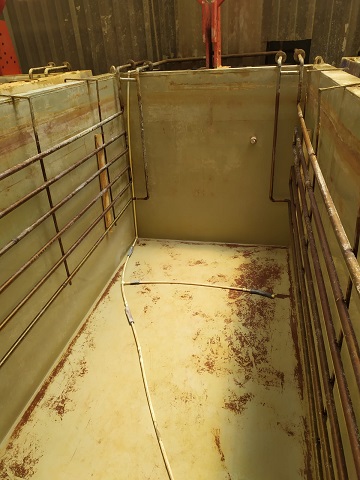
Activation solutions are slightly alkaline. It is sufficient and appropriate that the treatment bath material is made of standard steel material whose inner walls are coated.
Acid pickling baths must be made of acid-resistant material such as 316 type stainless steel. Alternatively, such pickling baths that do not need heating can be made of polypropylene material.
Phosphate coating baths should also be made of high quality stainless material since they are acidic. The same type of material should be selected for other elements such as heaters, nozzles, pumps.
Water Quality
The quality of the water used in the process baths and rinsing baths in the phosphating lines has a certain importance. Generally; It is suitable to use mains water in degreasing, acid cleaning, activation, phosphate coating and post treatment baths because it is economical. Nevertheless, very hard water should not be used in order to prevent the bath active ingredients from complexing with the ions in the water and losing their effect. Care must be taken that the conductivity value does not exceed 600 µS/cm.
In phosphating processes before painting, it is necessary to use deionized or low conductivity water before the last rinse. In case of using hard water with high conductivity, blistering may occur under the paint.
Regular water additions are made to the process baths operating at high temperatures to compensate for the loss of water due to evaporation. If it is hard water, over time, calcium and magnesium salts will accumulate. Depending on the properties of the treatment bath, the formation of such salts that cause quality loss should be prevented.
Phosphate Sludge Formation and Its Cleaning
The +2 valence iron (Fe+2), which is formed as a result of the etching reaction in the phosphate coating solution, is converted to +3 valence (Fe+3) thanks to oxidizing additives. It is mainly iron III phosphate (FePO4) which is called as phosphate sludge. This sludge formation should be removed from the phosphating bath periodically or continuously in order not to decrease the quality of the coating.
In simple terms, sludge cleaning is done by decantation method. The bath solution is rested and the sludge layer is collected at the bottom. The upper clear part is then pumped into an empty tank. After the sludge in the phosphate coating bath is cleaned, the clean solution taken into the empty tank is pumped back again.
Continuous sludge cleaning is done using a filter press. The bath solution is continuously filtered and recycled without sludge. The sludge accumulated in the filters should be stripped from the filters at regular intervals.