Zinc Phosphate Coatings
We can divide zinc phosphate coatings into three sections according to application areas:
- - Application for preventing abrasion caused by friction before metal forming processes such as cold drawing, cold forging, deep drawing,
- - Application for increasing paint adhesion before electrostatic powder coating and wet painting,
- - Application for increasing wear resistance and corrosion resistance with protective lubrication.
When used before forming of metals, coating weight of 5 - 15 g/m2 is usually required. It is most commonly used in wire and tube drawing processes. The phosphate layer is firmly attached to the metal surface and reduces friction in the dies and molds during the cold drawing process, allowing these operations to be carried out easily.
The phosphate layer remaining on the surface after the drawing operation creates high corrosion resistance during storage and transportation and prevents rusting. Phosphate coating is of great importance in high carbon wire drawing industry such as steel rope, spring, welding wire, pc wire, pc strand production. It provides continuity on the surface for multiple drawing operations and enables high drawing speeds. It enables difficult cold forging operations in the production of bolts and screws and ensures long service life of molds.
If zinc phosphate coating will be applied under paint, a coating in the range of 2-6 g/m2 must be obtained on the metal part. Making a uniform coating with thin crystal structure is important in terms of adhesion to paint and to provide corrosion resistance in harsh environmental conditions.
The desired coating weight for protective oil application is in the range of 10-35 g/m2. Zinc phosphate coating with coarse crystal structure and high coating weight retains the protective oil and provides an effective corrosion resistance. It is widely used for auto parts, fasteners and machine parts.
Zinc Phosphate Coating Products and Chemicals
Concentrated coating products are usually in liquid form, clear, colorless, light green or dark green. Activation and acid toner additives are powder products and are sold in 25 kg sacks. All products are packaged and sold in plastic drums or IBC tanks that are resistant to chemicals and comply with international dangerous goods transport rules.
Zinc phosphate coating products with accelerator system used for wire and tube drawing. It is suitable for immersion and continuous (in-line) use. Allows high speed drawing of carbon steel wires. Coating weight is in the range of 6-10 g/m2. High density and low consumption rate products with low sludge formation.
Zinc phosphate coating products with accelerator system used for wire drawing processes. It is suitable for immersion and continuous (in-line) use. It has a low amount of accelerator usage and sludge formation is very low. Coating weight is in the range of 6-10 g/m2. Products with high density and low consumption.
Products that are used for wire drawing before bolt and screw production works, by controlling the iron concentration without using additional accelerator products and providing a coating weight of 8-15 g/m2. It is preferred for demanding cold forging processes that require high coating weight after skin-pass drawing.
It provides phosphate coating which is necessary in demanding cold forming works in the production of bolts, nuts, screws and similar fasteners. Iron concentration of the phosphating solution is monitored and controlled by air mixing system. They are high density and low consumption products.
Used just before immersion zinc phosphate coating stage. Provides fine crystalline uniform coating. Can be used in pre-painting zinc phosphate and wire/tube zinc phosphate coating lines. High paint adhesion and high corrosion resistance is achieved by using in the phosphating line before painting.
It is used with accelerator in dipping zinc phosphate coating lines for iron and steel materials. With 2-4 g/m2 coating weight, it provides high corrosion resistance and good paint adhesion before powder coating and wet painting applications. Due to its fine crystalline coating feature, no activation is required.
One-component product suitable for iron, steel and especially cast materials. Used in immersion zinc phosphate baths without the need for accelerators. No need to use an activation bath as it forms fine crystalline coating. Provides good adhesion and high corrosion resistance for electrostatic powder paint and wet paint.
Easy-to-use one-component product for iron, steel and cast materials. It is generally preferred before powder paint and wet paint applications. It is used without the need for an accelerator. When used with activation, very high corrosion resistance and salt spray test results are obtained for the parts to be painted.
It is used in spraying zinc phosphate coating systems. Slightly alkaline powder product that provides a fine crystalline, uniform and dense coating. It is used together with zinc phosphating in wet paint, powder paint and cataphoresis painting. It is an effective product for high paint adhesion and advanced corrosion resistance requirement.
Products used in spraying tri-cation zinc phosphate coating systems. Suitable for iron, steel, cast iron and galvanized materials. It is used especially before cataphoresis painting and preferred for jobs requiring high corrosion resistance. Coating weight is in the range of 1.5-3.0 g/m2. It forms a fine crystalline, tight and homogeneous coating.
Products used in immersion type tri-cation zinc phosphate coating lines. Suitable for iron, steel, cast iron and galvanized materials. Ideal for cataphoresis, wet paint and powder coating. It provides high corrosion resistance. It creates a uniform zinc phosphate coating in a thin crystal structure.
Suitable products for spray lines providing thin crystal structure, low coating weight zinc phosphate coating for iron and steel materials. It provides high corrosion resistance with strong paint adhesion on the surface before powder coating and wet painting. Coating weight is in the range of 2.0-3.0 g/m2.
It is an easy to use one-component product used by dipping before protective lubrication. Suitable for iron, steel and casting material. Forms a medium - heavy crystalline zinc phosphate coating in the range of 10-20 g/m2. After phosphating, the parts enter the protective oil bath and become rust resistant for a long time.
Thick crystalline, heavy zinc phosphate coating products for iron, steel and cast parts by dip application method. Coating weight is in the range of 20-35 g/m2. Thick crystalline coating adsorbs a large amount of protective oil on the surface, and good protection against corrosion is achieved.
Zinc Phosphate Coating Images
Zinc phosphate coating color varies according to the properties of the phosphating chemical and metal material alloy. The appearance is in the range of light gray and dark gray on steel surfaces. After degreasing, phosphating and drying; grease, dusting and rusting should not be seen on the surface.
Thick/Heavy Zinc Phosphate Coating
Metal Surface Treatment - Phosphate Coating Images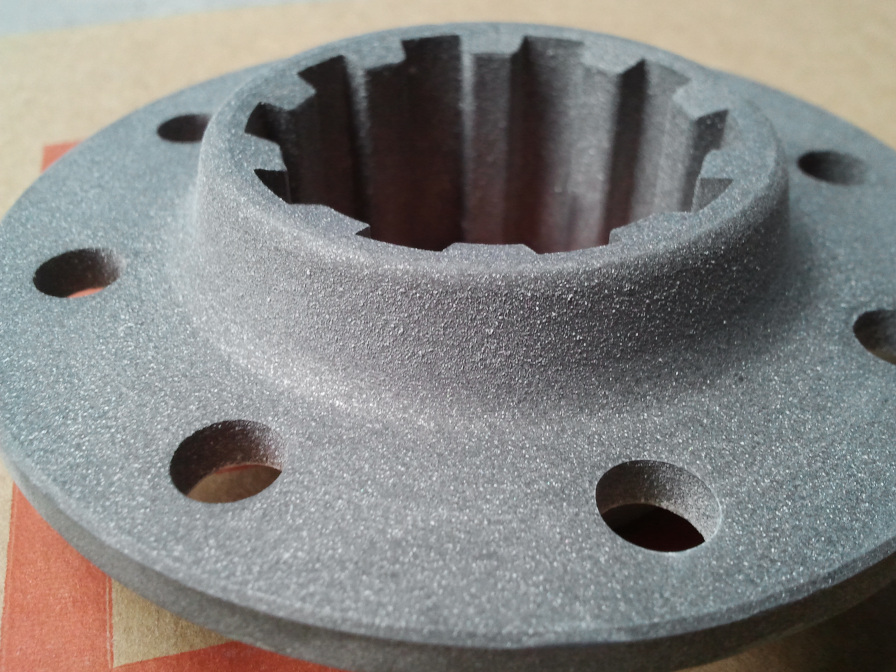
Notes:
* Thick crystalline zinc phosphate coating image suitable for protective lubrication.
* The coating was made with product PHORYL Z 29.
* Coating weight is 25-35 g/m², coating thickness is approximately 30-40 µm.
Zinc Phosphate Coating Reaction
Metal Surface Treatment - Phosphate Coating ImagesNotes:
* This video shows the zinc phosphate coating reaction at 60°C on a small steel piece surface.
* Coating process was done with product PHORYL Z 91.
* Coating weight is in the range of 8 - 12 g/m².
Zinc Phosphate Coating on Steel Wire Rod
Metal Surface Treatment - Phosphate Coating Images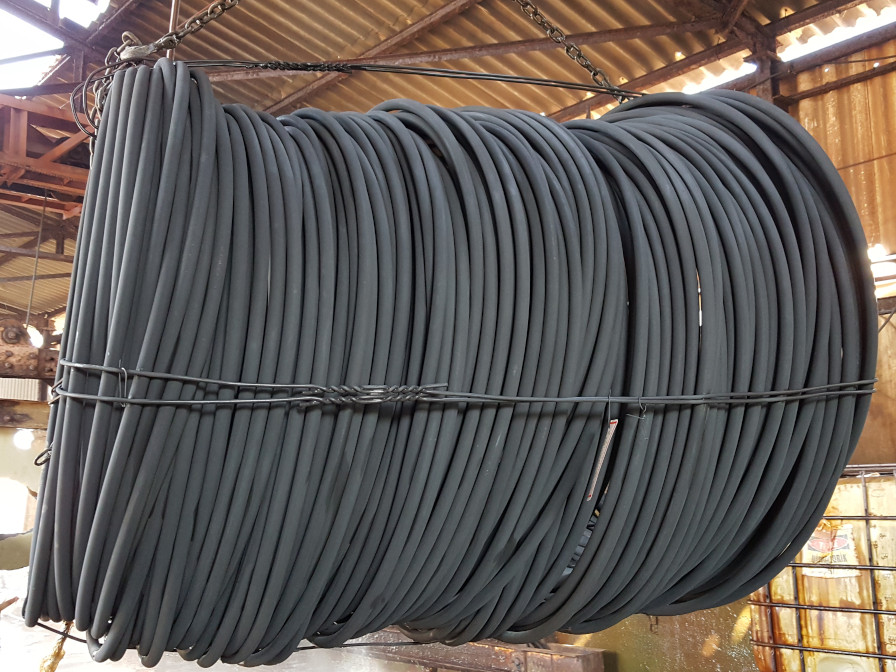
Notes:
* Zinc phosphate coated wire image suitable for cold drawing processes.
* The coating was made with product PHORYL Z 84.
* Coating weight is approximately 10 g/m².
Pre-Painting Zinc Phosphate Coating
Metal Surface Treatment - Phosphate Coating Images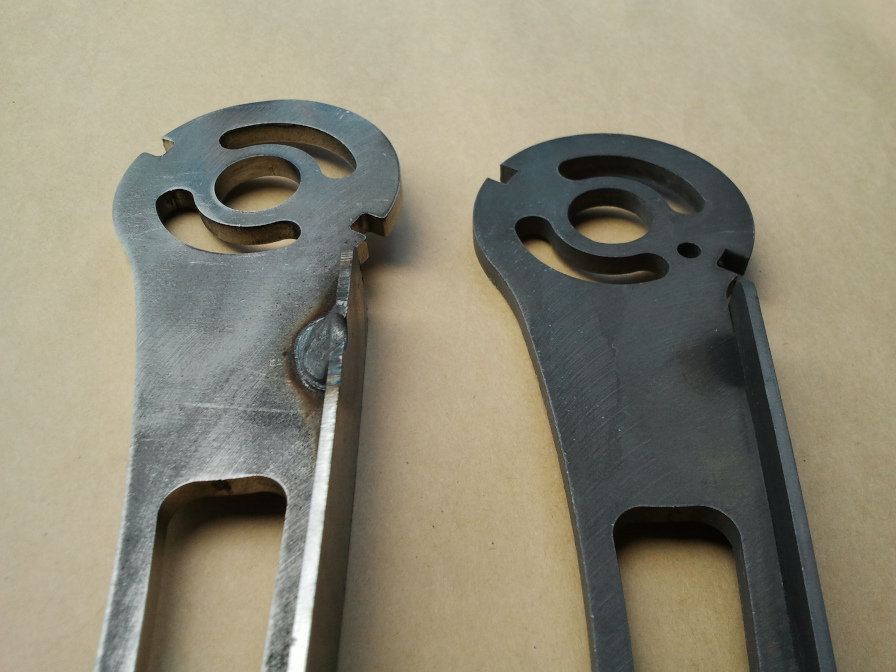
Notes:
* Images of the same steel work-piece without coating (left) and with coating.
* The coating was made with PHORYL Z 36 product, which creates a fine crystalline coating suitable for painting.
* Coating weight is about 3.0 g/m².
Zinc Phosphate Coating Scanning Electron Microscope (SEM) Image
Metal Surface Treatment - Phosphate Coating Images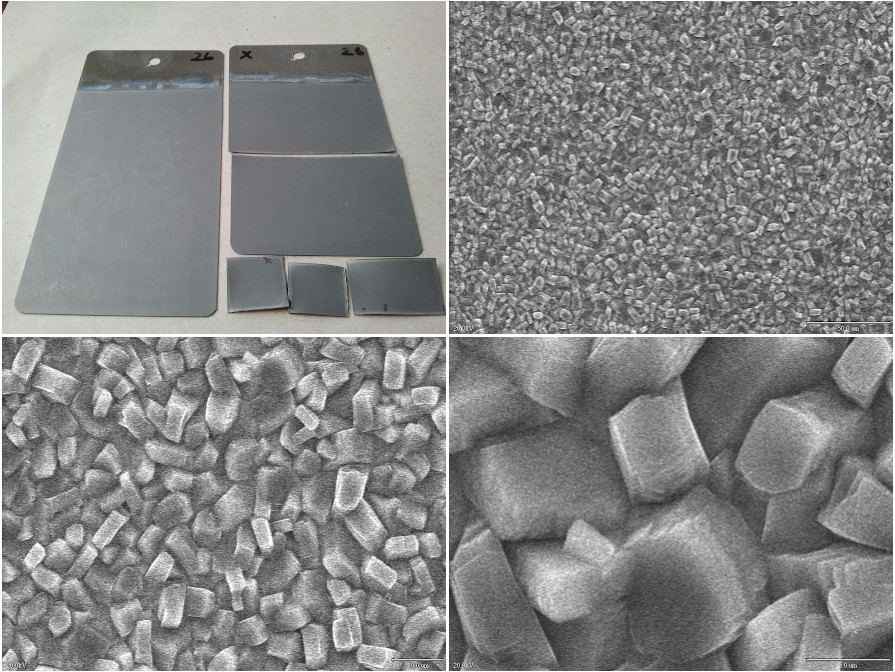
Notes:
* Test plate and electron microscope (SEM) images of thin crystalline zinc phosphate coating suitable for painting.
* Microscope magnification rates: x500, x1500 and x5000.
* The Coating was made with product PHORYL ZT 25.
* Coating weight is 2 - 3 g/m², coating thickness is 2 - 3 µm.