Zinc phosphating, which is used as under paint, is preferred in external parts and in the automotive industry. It is also widely used in the white
goods industry due to its high salt test and impact resistance. It is suitable for iron, steel and galvanized parts.
The parts must be cleaned from rust and oil in order to perform the zinc phosphating process well. It is not possible to make a proper zinc phosphate
coat on a surface with rust, grease, oil or dirt. For this reason, the parts are taken to degreasing before phosphate coating. Then, if they are rusty,
they enter the acid bath and are taken into the phosphating bath in a clean state.
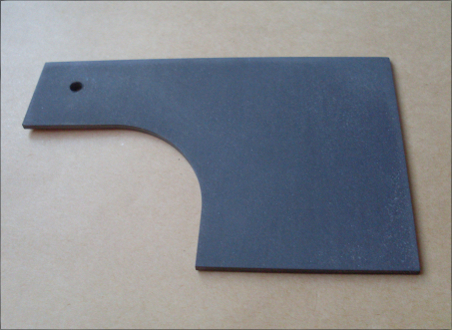
Zinc phosphate coating weight for under paint is 2-5 g/m². A fine crystalline and homogeneous coating should be obtained. If the coating on the metal
is thick crystalline and not homogeneous, activation should be used before the zinc phosphate bath. The activation bath affects the zinc phosphate crystal
size, making the phosphate coating thin and smooth. Passivation is used as a post treatment. Passivation process eliminates the problems that may occur
under the paint caused by water hardness. The salt layer formed under the paint weakens the adhesion of the paint and can cause the paint to tear.
Zinc phosphate process can be done in dip or spray baths.
In immersion zinc phosphate baths, 45 - 70 ºC temperature is sufficient. The application temperature in trication zinc phosphate baths is lower. Zinc phosphate
product concentration is in the range of 4-5%. The time required for phosphating can be 5 - 8 minutes. Treatment bath make up can be made with one-component or
three-four components. Tri-cation zinc phosphate coating provide high corrosion resistance. Usage is detailed. If cataphoric painting will be applied, the parts
are usually coated with tri-cation zinc phosphate.
Coating time can be kept lower with the effect of pressure in spray zinc phosphate lines. Bath make up concentration is lower than dipping process.
Accelerator and free acid regulator should be used for iron formed in zinc phosphate baths. Zinc phosphating baths will form sludge over time. The
sludge formed should be decanted periodically or taken out regularly with a filter system.
The parameters to be considered in zinc phosphate coating baths are temperature, bath concentration, total acid, free acid, time and accelerator point.
In addition, the drying temperature should not exceed 120 ºC. If it is over this level, it will damage the phosphate crystal form and cause loss of quality.