Zinc Phosphate Coating for Wire Drawing
In the wire drawing sector, zinc phosphate coating is applied by using of phosphating chemicals in dipping or continuous systems in order to facilitate, accelerate cold drawing processes and provide
high corrosion resistance in the drawn wires. During the cold drawing process, die damage caused by friction decreases and the wire drawing speed increases.
Wire must be cleaned from rust, oxides, and grease in order to make zinc phosphating well. It is not possible to coat zinc phosphate on a rusty, oily, wire. Therefore, an acid
pickling is used for pre-cleaning before phosphating. It is common to use hydrochloric or sulfuric acid in general.
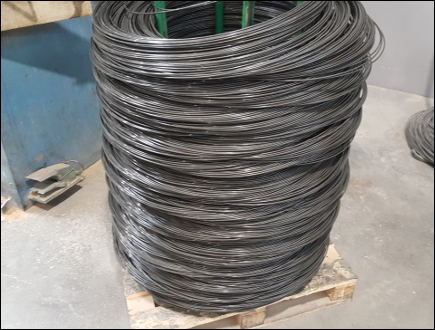
Zinc phosphate coating weight for wire drawing is usually in the range of 5-15 g/m². It is a fine and homogeneous coating that should be considered here. If the coating
on the wire is not fine crystalline or homogeneous, activation should be used before the zinc phosphate bath. With the use of activation, a thinner, dense and smoother
coating is obtained and coating continuity is provided for multiple drawings.
Wire coils are taken to the neutralization bath after phosphating. The aim is to protect the wire from rusting and to improve the transfer of lubricating dry soap into die
by providing salt formation on the wire surface.
For the calibration/skinpass drawing of low-medium carbon wires, it is useful to apply reactive soap at the last stage of the zinc phosphating line. Along with the high drawing
speed, high protection against corrosion is provided on drawn wire.
In wire drawing zinc phosphating baths, a temperature of 60-75 ºC is sufficient. Bath make-up concentration is in the range of 10-25%. The time required for phosphate coating
is between 3-10 minutes. Bath make-up and additions can be made with different products. In addition, accelerators or free acid modifiers can be used to reduce iron content in
zinc phosphate baths. Zinc phosphate baths form phosphate sludge over time. This sludge should be decanted at certain times or taken out continuously with a filter system.
The parameters to be considered in zinc phosphating lines are temperature, bath concentration, treatment time, accelerator point, iron point, phosphate point, total acid and
free acid values.