After the zinc phosphate, iron phosphate and manganese phosphate coating, ionic structures due to water impurities or hardness in the water rinsing
stage can hold on to the surface, salt formation occurs. This layer negatively affects the adhesion quality of the painted parts to the surface and
has a low corrosion resistance. Passivation treatment eliminates such problems, provides high corrosion resistance with good adhesion ability for the
painted parts.
In case of lubrication or any protective treatment instead of painting, high corrosion resistance is obtained on phosphate coatings. Salt spray test
results can be increased significiantly.
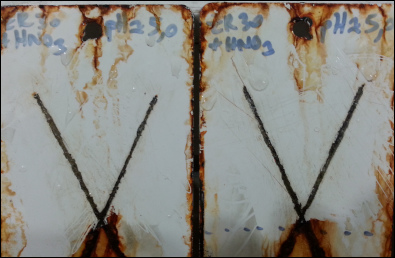
Liquid product that can be used both in dipping and spray baths after iron phosphate and zinc phosphating. It can be applied at ambient temperature. The pH of the passivation bath is between 4-6. The concentration of use is very low. It is more advantageous than Chrome +6 passivation in terms of ease of waste treatment.
Product that provides high corrosion resistance after zinc phosphate, iron phosphate and manganese phosphate coatings. It can be used as dipping or spraying. Application should be done in the temperature range of 20 - 50 ° C. Due to its chromium +6 content, it has to be discharged by performing the necessary waste treatment.
Powder product used by dipping method after zinc phosphate treatment in wire drawing and tube drawing industries. The neutralization treatment not only protects against rusting after zinc phosphating, but also creates a crystal layer on the surface that providing a better transfer of the dry soap lubricant into drawing die.