In this type of process, known as blackening or black oxidation, applied for iron, steel and cast parts, the parts are artificially oxidized as a very thin
layer in a hot alkali environment, and then protective lubrication is performed.
After oxidation process, a dark black appearance is obtained. Since the dimensions of the treated parts do not change, it provides an ideal corrosion protection
for dimension sensitive parts. It creates a more economical alternative to electrolytic coatings. It provides a good appearance together with corrosion protection
for machine parts. It is also common to use for various fasteners such as bolts and screws.
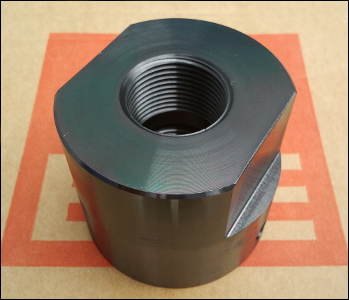
The operating temperature of the oxidation bath is in the range of 135 - 145 ° C. Application is carried out at this temperature while the solution is boiling.
Eeasy-to-use product that creates a black oxide layer on the surface of iron, steel and cast parts. Metal parts must be cleaned from rust and oil before blackening. After oxidation, metal parts should be rinsed with water and enter the protective oil bath.
Black oxidation product suitable for iron, steel and cast parts with different alloy and hardness properties. In the next stage, high corrosion resistance is provided by applying protective oil or wax. The surface should be cleaned well before blackening operation.
Oxidation product that provides an intense dark black appearance. Metal parts must be cleaned from oil, rust and other impurities before entering the blackening treatment. After blackening, the parts should be rinsed well with water and protective application should be done for corrosion resistance.