Alkali degreasing process can be applied by different methods such as spray, dipping, ultrasonic. It is suitable for iron, steel, aluminum,
zamak, copper and brass. Although it is problem free for iron and steel, it may be necessary to prevent abrasion in cleaning metals such as
aluminum and brass.
Alkali degreasers generally operate in the temperature range of 50-95 ° C. Effective cleaning may not occur at low temperatures. Therefore,
the temperature of the process solution is important.
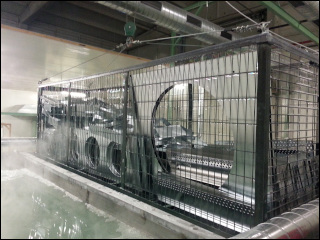
Dipping degreasing baths generally consist of alkaline degreasing chemicals. Along with high alkalinity and temperature, degreasing process is performed
on metal. It is suitable to use before iron phosphate, zinc phosphate and manganese phosphate coating baths. Degreasing additives can also be used to
increase the effectiveness of such baths.
In spray degreasing baths, there is an additional pressure difference compared to dipping baths. Thanks to the pressure, the cleaning effect is maximized.
Bath temperature is lower than dipping systems and process time is shorter. Appropriate degreasing chemical should be selected according to the type of
metal and the amount of oil/grease on it. It can be used in iron, steel, copper, zamak, brass, aluminum and galvanized parts.
Ultrasonic degreasing baths remove oil on metal parts with the help of sound vibration, chemical effect and temperature. In general, it can work with neutral
degreasing chemicals as well as working in medium alkaline environment. The bath temperature is not high and the processing times may be longer depending
on the amount of grease layer on the metal.
It is a highly alkaline and easy-to-use product used for cleaning dense oil layer before phosphate coating baths. It can be used in a bath concentration of 4-6%, at a temperature of 70 - 90 ° C and for a period of 5 - 8 minutes. It is a chemical suitable only for iron and steel.
It is used in degreasing baths in the coating industry. It can also be used as pre-degreasing in phosphate coating lines. It is applied at a concentration of 5-10%, at a temperature of 70 - 90 ° C and for a period of 5 - 8 minutes. It is a suitable chemical for iron, steel and casting.
It is used with dipping method to remove oil, grease and impurities from aluminum surfaces. Does not cause darkening. Also suitable for metals such as copper and brass. It is applied at a concentration of 3-5%, at a temperature of 60 - 70 ° C and for a period of 5 - 8 minutes.
It is an alkaline product used in ultrasonic degreasing baths in metal industry. It can be used in iron, steel, copper, gold, zamak, brass, aluminum and galvanized parts to remove heavy oil/grease layer without blackening.
It is a silicate-free, powder form product that can be used in spray phosphate coating lines, has a high degreasing and cleaning effect. It is ideal for iron phosphate and zinc phosphating lines. It can be used for degreasing in iron, steel, cast iron and galvanized parts.
It is a silicate-containing alkaline powder product with high degreasing effect used in spraying systems. It protects the metal against short-term rusting. Ideal for use in industrial parts washing machines. It can be used for all metals and does not make any darkening on treated parts.
It is an alkaline degreasing and phosphate removal product suitable for dipping and spraying systems. Especially in the fastener industry, it is ideal to use the parts for degreasing and de-phosphate processes before heat treatment furnaces.
It is used as an additive for cleaning heavy oily and greasy parts in alkaline immersion degreasing baths. It is sufficient to use as low concentration as 0.1 - 0.5%. Thanks to its surfactants and emulsifiers, bath effectiveness is increased.