Along with cleaning ability, acidic degreasing is also applied for parts that require oxidated layer removal. This type of products should be used
as rust and scale cleaning can be accomplished with acidic chemicals. It can be used for aluminum, iron, steel, zinc alloy parts.
Although acidic degreasing baths can work without the need for heating, degreasing and rust removal would be more effective if it runs at slightly elevated
temperature.
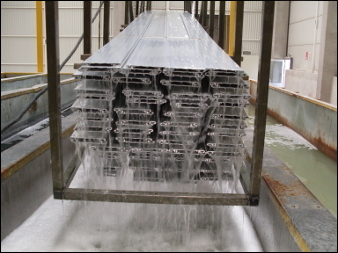
The general ingredients consist of surfactants, emulsifiers, inhibitors and acids (phosphoric, sulfuric, hydrochloric, hydrofluoric, etc.).
Bathroom equipment should be made of PP or stainless as the process solutions have strong acidic properties.
It is possible to work in concentrations of 5 - 50% depending on the contamination of the metal surface. The processing time increases as the concentration
of the bath decreases. Although high temperatures are not required, heating may be recommended in certain situations, as this will increase the reaction rate
with heat. The points to be considered in acidic degreasing baths are total acid and application time. Decreasing the bath concentration lowers the rate of
degreasing and replenishment is required.
Abrasion of iron and steel parts can be prevented by using inhibitor containing products. Acid inhibitor minimizes metal wear after rust and scale removal
on the metal and extends the life of the treatment bath. Acid inhibitors are generally not required for aluminum surfaces, since slight abrasion is required.
It is a phosphoric acid based rust remover and degreasing material that can be used with dipping and hand brushing method. It has the feature of cleaning oxidation layer and rusting on the metal at the same time. As it can work at ambient temperature, its efficiency will increase in slightly elevated solution. It is ideal to be used in 10-20% concentrations.
It contains acid mixtures, emulsifiers, inhibitors and wetting agents. It provides degreasing and rust cleaning from the metal surface. In phosphating lines, rust removal can be achieved by using between degreasing and phosphate coating stage. It is ideal to be used in 10-40% concentrations. It is suitable for iron and steel materials.
It is a degreasing product used in immersion aluminum chromate processes. The treatment gives a suitable surface for chromate coating and subsequent painting by providing proper degreasing and etching. 2-5% concentration, 20-50 °C temperature and 2-10 minutes processing time are ideal.
Degreasing material used before chromating and for general aluminum cleaning. It can work at ambient temperature. Provides a better cleaning in slightly hot solutions. Foam formation is low. It provides suitable surface prior to chromate coating. It is applied at a concentration of 3-5%, at a temperature of 20-50 °C and for a period of 2-7 minutes.
It is a product that provides etching and surface cleaning of aluminum materials by immersion method at ambient temperature. It cleans the aluminum oxide layer by etching with acidic effect and creates the surface suitable for chromate coating. It is suitable to use after alkali degreasing.
It is an acidic degreasing product used at the beginning stage of hot dip galvanizing lines. It performs pre-etching of steel and iron parts together with degrerasing and soot cleaning before acid pickling. Due to being an acidic product, the treated parts can pass directly to the acid baths without rinsing. It is suitable to use in a concentration of 5-10%.